بهترین گریس برای چکش تخریب
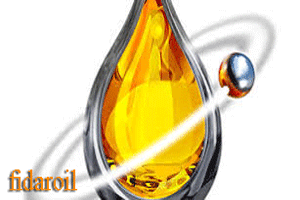
بهترین گریس برای چکش تخریب چیست؟
بهترین گریس برای چکش تخریب چیست؟ گریس ماده ای نیمه جامد است که به صورت معمولی و نسوز تولید می گردد و برای ابزارالاتی مثل مینی فرز، چکش تخریب و… استفاده می شود. این قطعات تحت دور بالا و فشار کار می کنند و برای جلوگیری از کاهش ساییدگی و فرسودگی زودرس، بایستی از آن محافظت کرد. یکی از راه های محافظت از قطعات چکش تخریب استفاده از گریس نسوز با پایه لیتیوم است.
اگر محیط کار شما آلوده یا در محیط مرطوب قرار دارد، بهترین گریس برای چکش تخریب، گریسی است که با مواد مقاوم در برابر آب یا مواد شیمیایی می باشد. پایداری در برابر آب و دمای بالا، جلوگیری از اصطکاک، پایداری کیفیت در زمان مصرف از جمله مهم ترین خواص این محصولات بوده که همین موارد سبب کاربرد گسترده آنها گشته است.
چکش تخریب با سرعت بالا جهت شکستن مصالح سخت مانند بتن، آجر و سنگ استفاده می شوند که برای عملکرد بهینه، حفظ قدرت و جلوگیری از گرما و ساییدگی از بهترین گریس برای چکش تخریب با خصوصیات زیر استفاده گردد:
- کاهش ساییدگی و اصطکاک: از گریس نسوز با خواص ضد سایش استفاده کنید تا اصطکاک بین قطعات را تا حد امکان کاهش دهید.
- حفاظت در برابر زنگ زدگی: گریس لیتیوم در برابر رطوبت و خوردگی از زنگ زدگی قطعات جلوگیری می کند.
تفاوت چکش تخریب گریسی و روغنی
چکش تخریبی به دو صورت روانکاری می شوند: گریس و روغن. چکش تخریب گریسی نیازی به پر کردن مداوم محفظه ندارد و روانکاری در فواصل زمانی طولانی تری انجام می شود. اما در نوع روغنی، پس از اتمام روغن سریعا باید شارژ شود.
تفاوت دیگر چکش تخریب گریسی و روغنی در روانکاری در شرایط آب و هوایی سرد است که نوع روغن عملکرد بهتر در برابر یخ زدگی دارد، ولی میزان قدرت چکش گریسی بالاتر بوده و قیمت آن هم بیشتر از روغنی است.
ویژگی های گریس مخصوص چکش تخریب
گریس مخصوص چکش تخریب یا سایر گریس ها با توجه به ترکیبات و خاصیت ضد دما و فشاری که دارند، در جنبه های مختلف به کار می روند تا در زمان فعالیت برای تجهیزات مختلف عملکرد مطلوبی داشته باشند. با این حال نمی توان از آن ها انتظار خنک کاری را داشت تا دمای کارکردشان پایین بیاید. از این رو تنها به منظور خنک کنندگی نباید از آن ها استفاده کرد.
مهم ترین ویژگی های گریس مخصوص چکش تخریب عبارتند از:
- سادگی در طراحی سیستم های روانکاری
- ماندگاری بالا در محل روانکاری
- کامل تر شدن آب بندی سیستم ها، کاهش نشتی و چکه کردن روانکار
- بهینه سازی چسبندگی این روانکار به قطعات در شرایط دما و فشارهای بالا
- سهولت و آسودگی در مصرف
- کاهش دفعات روانکاری با گریس
- توانایی تحمل فشارهای سخت و سنگین
ترکیبات و گرید گریس چکش تخریب
گریس چکش تخریب از ترکیب روغن پایه، ماده غلیط کننده یا سفت کننده و انواع مختلفی از افزودنی ها یا بعضی از صابون های شیمیایی ساخته می شوند. این گریس ها در رنگ های متفاوت با برندهای گوناگون تولید می گردند که با توجه به گرید (nlgi) و نوع موادی که در آن استفاده شده در تجهیزات تحت شرایط مختلف استفاده می شوند.
گرید گریس چکش تخریب از 000 الی 6 می باشد که هر چقدر به عدد 6 نزدیک تر باشد؛ گریس شما غلیظ تر شده و هر چه به 000 نزدیک تر باشد، گریس رقیق و مایع تر خواهد بود. معمولا گریس هایی با گرید 2 یا 3 برای چکش تخریب استفاده می شود. برای انتخاب گرید مناسب و تعیین بهترین گریس برای چکش تخریب به موارد زیر دقت نمایید:
- قوام گریس که اگر گرید آن عدد پایین تری داشت روان تر است و عدد بالاتر نیز غلیظ تر خواهد بود.
- نوع باری که گریس از نظر ضربه، فشار و سرعت تحمل می کند.
- دمای کارکرد گریس برای روانکاری مهم است.
- سازگار با نوع فلزاتی در دستگاه استفاده شده است.
- شرایط محیطی را از نظر رطوبت، مواد شیمیایی، دما و… را در نظر بگیرید.
گریس کاری دریل چکشی
برای گریس کاری دریل چکشی چه اقداماتی را باید انجام داد؟ ابتدا گریس مناسب چکش تخریب را تهیه نموده و بهتر است برای عملکرد بهتر، دفترچه راهنمای چکش را بررسی نمایید یا از یک متخصص کمک بخواهید. گریس کاری منظم و دوره ای باعث شده تا چکش با نرمی بیشتری کار کند و از حرارت زیاد جلوگیری کند.
در صورتی که با حرکت سخت قطعات، کاهش قدرت ضربه، صدای ناهنجار و گرم شدن بیش از حد دستگاه مواجه شده اید، خواهید دانست که زمان گریس کاری فرا رسیده است. به طور معمول گریس کاری این تجهیزات هر 100 الی 120 ساعت انجام می شود که آن هم بسته به شرایط کارکرد آن دارد. گریس کاری دریل چکشی نیاز به رعایت اصولی است که در طی مراحل زیر به آن اشاره می کنیم:
- برای ایمنی بیشتر و جلوگیری از حساسیت های پوستی، از دستکش و عینک استفاده نمایید.
- دستگاه را خاموش نموده و گریس قدیمی را از محل روانکار قبلی پاک کنید.
- حال بخشی از گریس را به محفظه دستگاه که مربوط به گریس است را اضافه کنید.